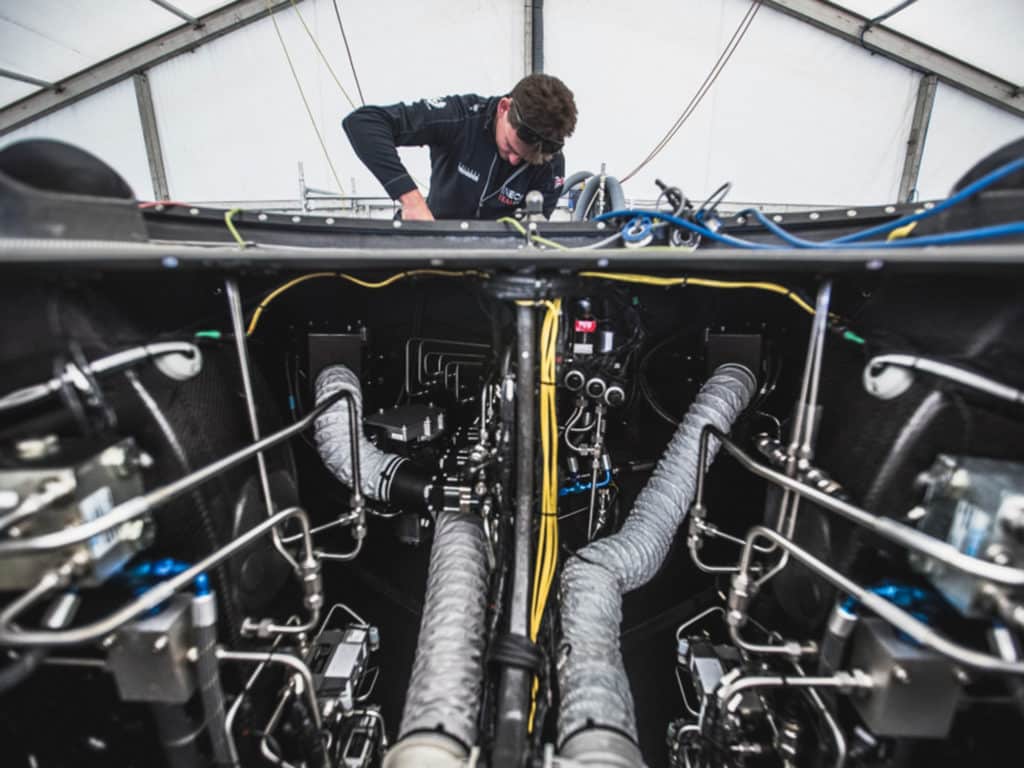
Every racing sailboat needs to be both strong and light, but only a handful of them need to be strong enough to cope with a crash landing, coming off the hydrofoils at 50-plus knots. Images of the first-generation AC75s, in some spectacular touchdowns have already hit the internet—and those are the wipeouts teams have been willing to share. There will be a lot more before the Cup is won and lost.
It’s an interesting time to be a structural engineer with an America’s Cup team. It would be hard enough if the challenge was to simply build the AC75 with sufficient strength to handle the big crashes. However, the AC75 is a difficult boat to keep under the maximum weight allowed by the rule, and the need to keep it light puts additional pressure on the structural engineers.
“We start by hiring the best engineers we can possibly find, that’s a big part of it… a big structural failure at the wrong time could end the campaign, so they are absolutely critical people to a successful Cup campaign,” says INEOS Team UK skipper and team principal Ben Ainslie.
Building a safe but light structure starts with having a deep understanding of the loads and the stresses the boat will experience. The teams get this by modelling the boat in structural analysis software, which is a challenge unto itself because the AC75 is a completely new concept, a new type of boat. The team can apply experience from other similar boats, but there is no direct knowledge of what’s worked before.
“There are three different cases, and they get harder,” Ainslie says. “The first set are when the boat is sailing in a straight line and the loads are relatively well understood. We can model this with the Velocity Prediction Program and other tools and get a pretty good idea of what’s going on.
”The second set of cases is what we could call the planned maneuvers, where there are dynamic loads in the bearaways and tacks and jibes and so on. Again, we can model these and run various simulations to get a good idea of what’s happening.
“The last case is the hardest, and that’s the unplanned maneuvers such as crash downs and wipeouts. This is the hardest because at the beginning we had no experience of quite what these would look like, and even now our experience is very limited. We can do some calculations and we can do some simulations, but it’s much harder to be confident that we have covered every possible case.
It’s a curious thing about modern engineering; the tools and methods available to analyze the stresses in a structure are very sophisticated and accurate. So, if the maximum stress was known precisely, the boat could be designed with similar precision. Unfortunately, no one can be completely sure about the loads a boat will see because this relies on modelling its behavior in all circumstances.
This is why the design has a safety factor; an extra load the structure is designed to withstand beyond the expected load that’s predicted by the modelling—but where do these safety factors come from?
”They’re not guesstimates. There’s a lot of attention to the detail,” Ainslie says. “They represent the worst case in all the previous calculations of the stress on the boat. The engineers add up the uncertainty in each step of the calculation and get to a number of how far they could be out. And then this number is added as the safety factor.
“This is where experience really comes into it, knowing across a wide range of boats and conditions how well the safety factors have worked before and then being able to make a judgment on how good they could look in this particular case.”
Once the loads are understood, the engineers can start designing the boat. “There are some general decisions to be made on things like the core material for the main panels, and the type of thickness of carbon that will be laminated on either side to create the composite structure.
”We do a lot of testing with the different potential materials and build the test panels to be confident that we made the right decisions. Then the internal structure of the boat is a big decision, working out where the bulkheads and the beams will go to support the panels. And of course, this is also impacted by the shape of the hull. The engineers have to be very aware of the work that’s being done by the naval architects.
”There’s also a huge amount of detail work for every part of the boat that will be separately loaded, everything from the rudder fittings through to the support structure for the mast. Each part has to be considered in view of the loads it will suffer in every circumstance, and every time we find a solution that’s strong enough, we have to start again to see if there’s a lighter way of doing it. There’s a lot of iterations to the design process.”
It’s a process that rewards precision and attention to detail, but also creativity – not always attributes that are found in the same person. “It’s the new and original creative solutions that can end up saving the weight,” Ainslie says. “It’s hard to find people who can do both well, and we also need a mix of both types to create a really, really good solution.”