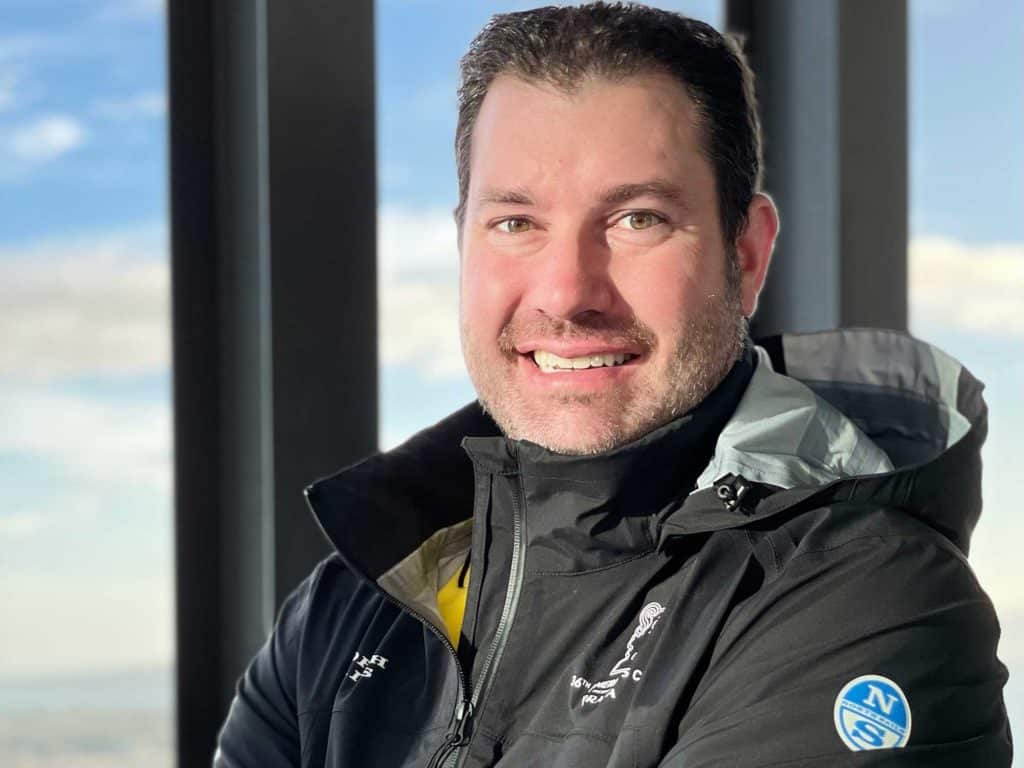
An enduring appeal of the America’s Cup is the inherent challenge of having well-funded teams full of very smart sailors, designers, builders and technologists face off against each other in a quest for an edge in performance that is often exceedingly narrow, yet can make all the difference between winning and losing. Whether racing in J Class yachts, 12-Metres, ultra-fast multihulls or the current foiled monohulls, any small edge in speed and maneuverability can make a huge outcome in the results.
It is this quest that drives innovation in design and fabrication, some of which may trickle down into the levels where the rest of us sail, and a team can devote enormous resources into this effort: reportedly the American Magic team logged more than 100,000 hours in design time put into their entry. Yet how do they know the limits on how far to push? Who is it that defines and enforces these limits? And how can teams be kept within the goalposts for compliance?
Not only are these tricky questions, but they have to be addressed correctly: the integrity and success of the event depend on it.
To explore these and other questions we had a chat with David McCollough, one of three members of the Measurement Committee for the 36th America’s Cup, while he was in quarantine in Auckland awaiting clearance to start working on site. He was dividing time between his family that had come with him for the next few months of the event, his ongoing projects at home with his yacht design firm McCollough Yachts in Newport, and his position as an AC36 measurer.
First, a preamble is needed on class rules. Most of us who are one-design racing know about these, and how they may (or may not) define specifications and limits to defined dimensions and materials used in the hull, appendages, rig and sails, along with other speed-producing parameters like crew weight. Most strict one-design classes are those that permit little or no changes to approved builder-supplied parts, and many of us know how to optimize our performance within these strict rules by, for example, fairing the bottom or maximizing our crew weight.
In contrast, other classes are more relaxed and permit some development to evolve within defined limits. This is where the AC 36 Class Rule is, where some parts of the boat are one-design and provided, whereas others are allowed to vary subject to the approval of the Class Rule Committee, whose eyes and ears for interpretation and compliance are the Measurers.
McCollough’s qualifications for AC36 started from when he was employed at Morelli and Melvin during the 34th America’s Cup where the team was commissioned by Oracle to help write the Class Rule for that cycle’s event. Educated in mechanical engineering and yacht design, he said that was a cycle that showed huge development change from starting with some non-foiling boats to having all foiling boats, with the game-changer being in the details of foiling control. He credits this time with having made the contacts and good relations with members of Team New Zealand that has led to his current appointment.
“This is where I learned about how tough rule-writing really is,” McCollough said, “and how challenging the job of Measurer is in an evolving environment. This has also allowed me to appreciate the process involved in this cycle with yet another new type of boat: you often don’t know what you don’t know because no one has dealt with a boat of this type before. Fortunately, for this Cup Cycle there has been an open dialogue, in the form of Rule Interpretations and Rule Amendments, between all the parties and the Rules Committee.”Members of this committee in this cycle include Stan Honey, world-famous navigator and sports media technologist, former World Sailing technical director Carlos de Beltran and composite structures expert Hasso Hoffmeister from DNV Germanischer Lloyd.
“We looked at everything in the boat: for rigs, we wanted them to be one-design, but they would need to be checked. For the FCS (foil control systems) built in New Zealand, we needed the same. And for the foil cant arms carefully built at Persico in Italy, used templates to make sure the one-design shapes are maintained.”
Provided cant arms are built in high-strength carbon composites and not only rigorously weighed and measured, but their strength is tested in deflection tests.
Another tight control is crew weight, which for the team of 11 is constrained to be between 960 to 990 kg.
As for sails, there is some room for development among the 90m2 headsails, 200m2 Code Zero’s and 135 to 145m2 double-skin mainsails even though these are limited in both number and sizing, with bar-coded stickers used to track the sails along with their dimensions. This helps McCollough and the other measurers to track which sails in each team’s inventory are being measured in and declared for use during each stage of the series.
Dimensions of the team-built foils are measured—for example, the max span on the rudder foil is 4.0 meters, the span on each cant foil is 3.0 meters—as are their intended draft: 3.5m for the rudder and 5.0m for the cant foils. Yet variations will be possible in more subtle aspects of their design, and likely to also be an important area for development.
What’s left is the hull and what’s in it to account for in the overall 6500 kg target weight for the entire boat. The hull dimensions may be measured and have fixed limits—20.7m long, 5.0m max beam with a 2.0m bowsprit—so variations will be in how the hull volume is distributed in shape. Much has been said already on these variations between skiff and scow-style shapes, which reflect for each team their unique interpretations of priorities in the hydro versus aero drag modeling: for example, whether to achieve some form stability while immersed during turns, or rely more on foiling for stability.
“Control for this aspect of the job is easier than it might seem,” said McCollough, saying that in this cycle there is heavy reliance on use of digital design files shared from the teams with the measurers to first check for compliance, then verified using laser cloud scanning technology. He said this in stark contrast to AC34 where the great amount of variation made the conforming process “seem like the Wild West.”
Once boats and their parts have been checked for rules compliance and approved, an ongoing issue is making sure they remain within the rules. McCollough says the measurement team has devised procedures that are simple—like simply weighing the crew—to more complex, such as hanging a mast with its sails to check compliance to both weight and center of gravity limits.
“It will be important to just continue our current level of open communication with the Rules committee and the teams,” he said. “By continuing this we should be able to efficiently resolve issues as they arise.”
A final question for McCollough is why agree to move to the other side of the world with your family to take on this role in what could be a contentious high-pressure environment? Being in the business of multihull design, he feels it has had direct benefits.
“It gives me a front-row seat to seeing all the developments in ideas and design, particularly in the aerodynamic field,” he said, having as he does total behind the scenes access to all the teams. He is using this knowledge in designing a line of foil-assisted power boats catamarans, and has a 125-foot performance cruising catamaran design in the works. And these lessons from the AC experience have not only helped in design trickle-down, but in the composite engineering and construction methods as well. McCollough explains, “It is already clear that McCollough Yacht’s New York based client for the 125 will benefit from what will be learned in Auckland.”
So, in this sense America’s Cup 36 is already fulfilling one of the event’s enduring traditions: breaking ground into new arenas that will benefit sailing technology.