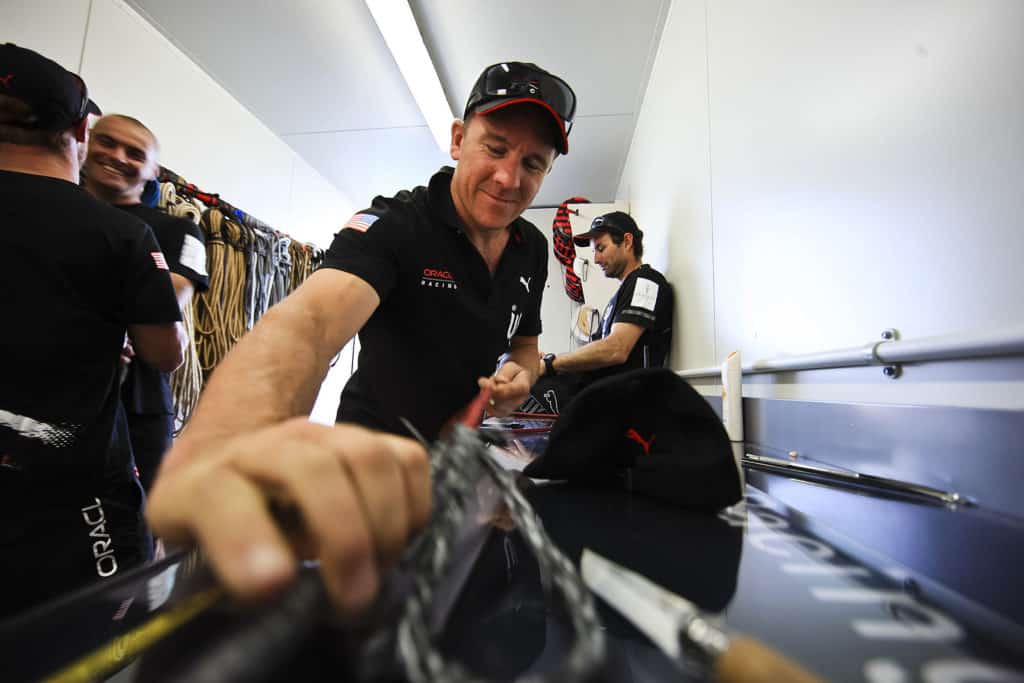
Andrew Henderson
There’ll be many things that stand out as being both outstandingly good and outstandingly bad about the current edition of the America’s Cup final match. Falling into the former category is that the races have gone off on schedule each race day with virtually no technical hitches or breakdowns—incredible really, given the extreme nature of the boats and the equally as extreme speeds and maneuvering witnessed on the racecourse (who will ever forget Emirates Team New Zealand’s near capsize?). While the sailors may like to keep sailing the AC72s for a while longer, the shore crew are ready for that vacation as AC34 begins to wind down. Simply put, keeping the AC72s on the water and in perfect working condition is a world-class production that requires countless hours.
From the outside it’s easy to wonder how it all gets done. Andrew Henderson, Rig Team Manager for Oracle Team USA, explains that there’s a rigid process in place that ensures the maintenance and development work is carried out as perfectly as possible. Henderson’s been a rigger for 20+ years and has his own rigging business back home in Australia. He’s worked for the Oracle team for the past four years and credits the guys he works with for the reliability of Oracle’s AC72: “They’re the top guys in their field and great to work with.”
What systems are in place to make sure all the work gets done?
AH: There’s a plan at the start of the regatta that we are following, and if there are items that are failing beyond what we expected, we need to make sure we’re keeping on top of those as well as the known items to be serviced.
What’s the process once the boat arrives back at the dock?
AH: As soon as the boat is back at the dock the sailing team gets together and comes up with a job list with any issues on the boat they’ve had during racing. That gets added to the master job list, which then gets circulated through all the heads of department, and then jobs are distributed out to the shore crew once the boat gets rolled into the shed and all the post-race checks are done.
The wing is separated from the platform, and one guy looks at the control systems, the structural engineers walks around it with a flashlight to check out the flaps, and the sailmakers check out the panels of clysar (shrink film that goes over the wing). When we initially set up for a start of a regatta like this there’s a big visual inspection on the wing, sometimes we run it through a camera. Next up is the platform which gets thoroughly inspected for any weak areas. The rudders and daggerboards are taken out for bearing checks and service.
What does the post-race checklist involve?
AH: Each department has a folder they go through—rigging, for example, will check all the terminals in the boat, all the individual components for the wing, the structural system for any cracks or known “wear” areas. That check takes place before the final job list for the day is put out. If we come across any problems there, we start working on those and off we go into the night.
How often has there been issues post-race that have had to be dealt with?
AH: Other than that there’s just a lot of stuff to maintain every day, we haven’t had any issues with the operating systems on the boat or the ways that the guys sail the boat, so that’s been good. But, on the flip side, this has been a massive development program, more than we’ve had in a while so that’s been a huge amount of work. So, while the wear and tear on the boat hasn’t been bad, and I think the sailing we’ve done until now has ensured that everything is in place and hardy enough to get through the regatta, it’s been the big list of development items that’s kept us busy. We’ve sailed every day except one this past month and the shore crew hasn’t had a day off in a month.
Does the boat get cleaned and polished after racing?
AH: Not really, we’re not getting it ready for a boat show. We’re more focused on making sure everything works. The night shift guys may have time to do that kind of detail. Of course the foils get some attention but in terms of in terms of trying to make it shiny, that doesn’t happen. [Note—ETNZ cleans and polishes its boat after every race day and following maintenance, it goes into “lockdown” at 7 p.m. after an intruder was found climbing over the fence to the ETNZ boatyard at Pier 32 some weeks back.]
How many guys are involved in getting the boat in and out of the shed pre/post race?
AH: We have about 30 guys involved in the lift and the launch project, which starts pretty early in the morning, and same thing in the afternoon, about 30 people. If there’s a big issue that needs more hands, we have around 50 people we can bring together.
Who makes up the night shift?
AH: Mainly the boatbuilders at this stage. A team comes on at 4:30 p.m. and work through until about 6 a.m. Any issues, structural or otherwise, for example there are lots of fairings on these boats which require constant attention so the guys are often working on the fairings, making sure the boat is structurally sound so it’s ready to go for the next day’s race.
When and how does the measuring of the boat take place on race days?
AH: We have the wing weighed at the end of the day which takes about half an hour. The following morning the measurers show up again and weigh the platform with the wing measurement. The measurers are at, or around, the boat from the minute we roll out in the morning until we start the race.
What happens between races?
AH: We have a team that gets on the boat – one guys checks the control system on the wing, someone checks all the moving parts like the blocks, the hull is checked, the [hydraulic] oil levels are checked, the electronics are checked for shorts—we probably have about 10 guys who jump on between races to make sure it’s ready to go for another round.
From the shore team’s perspective, do you feel a responsibility to the sailors once the boat docks out?
AH: Absolutely. My area is rigging, and for any major rigging failure there is massive potential for someone getting hurt so we certainly think about it a lot. We do have processes where we do all the checks, and we’ve done a lot of testing to make sure that the guys sailing the boat are comfortable with the rigging, for example.
How is the decision to make improvements to the boat conveyed to the shore crew?
AH: There’s a huge amount of data and a performance team that drives the backend. The sailors come back with their ideas, the designers and engineers come up with a plan, and we get a job list from that, we do the work, and then the guys go sailing. That’s what we’re doing today. It’s continuous, and you don’t always know where the end is, but everyone knows that now we have just a few days to go, maybe a week, and so we have to do as much as we can this week to try and win races.
Are these boats just a massive undertaking to you?
AH: It’s a huge project. We’ve done big maxi boats but nothing on this scale—the people, the technology … it’s mind blowing. These boats are fantastic, and it’s a great thing to be involved in. We have a great working environment, we’re given the tools to make our work safe, and the time to make it safe, so that’s reassuring.