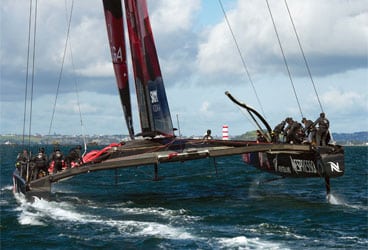
ETNZ thumb
“It’s far more complex than anything I’ve ever been involved in,” says Nick Holroyd, Emirates Team New Zealand’s technical director. Holroyd, who’s been in the America’s Cup game since 1997, is tasked with overseeing the collective brainpower of more than 30 engineers, designers, and programmers—all tied together in a complex web with the AC72 catamaran in its center. The end game is to usurp the Auld Mug from its formidable defender, Oracle Team USA, but the playbook is wide open. Wings, hulls, hydrofoils, rigging, electronics, and manpower are the core elements of these new craft, but for each known entity, says Holroyd, there is another unknown. In an exclusive interview following the August launch of Emirates Team New Zealand’s first AC72, Holroyd explains where they’re at with the first of their two boats, and where they may go before next summer’s Louis Vuitton Cup.
When you were handed the AC72 rulebook, where did the team begin, and where did you put your efforts straightaway?
Intuition tells you that there are areas where you think you’re going to find big gains. The wing is an interesting one. Structurally, it’s quite complex, but making it easy to use on the water so that you can get optimal shapes easily and repeatably is important. The aircraft industry has bequeathed us a lot of knowledge already, so the aerodynamics of the wing is not as complex as you might think. With the platform, what’s important is to quickly get to a level where your velocity predictions are good. Once you get to that level, you can start looking at the drag breakdown, and that denotes where to put your effort. We have to put more effort into the bigger ticket items like the wings and platforms, which require longer lead times to design and build.
With a compressed racecourse on San Francisco Bay and relatively short legs, how do you weigh straight-line speed versus faster maneuvers?
A lot of the maneuvers will come down to the fact that you’re seriously understaffed in terms of the loads involved [with 11 sailing crew], so keeping systems simple is key. Boats that go fast in a straight line tend to go fast out of maneuvers as well. Bow volume, from what I’ve seen, is an obvious difference across the fleet so far. That dictates how hard you can lean on the boat coming out of maneuvers. Also, the ergonomics of the boat and the platform, and being able to handle the loads on the boat efficiently are critical.
What are the defining traits of your first boat?
This boat was designed long before the start time was known. We’ve gone with a boat that’s relatively sea-kindly and has volume features that allow it to be pushed very hard. Our boat, in terms of windage, is far from complete. All the fairings are still to come: The boat will look significantly different in race mode. One of the issues with putting all the fairings on the boat is that it makes a lot of the systems difficult to get at and tune, so we chose to put the boat in the water in a raw state to facilitate that development process. The launch date for our second boat is February next year, so we’re in the middle of tooling up for that boat. We’re later than we wanted to be. I’m sure everyone else is late as well.
A multihull of this scale is a complicated structure; explain what you have going on under the boat.
Ours and Artemis are on a similar model with a diagonal structure in the back of the boat, which acts as a truss and stiffens it torsionally a great deal. Tornado sailors will say torsional stiffness is paramount, but the price you pay is more under-rigging and under-structure. A lot of choices come down to stiffness versus windage. Windage is easy to quantify, but torsional stiffness is a lot harder, so this is one of the hardest tradeoffs to put a number on.
How do you spread pedestals and deck gear around?
With the wing on this thing, righting moment is impossible to ignore, so we’ve split all of our deck gear between the two hulls. We sail with 11 up on the weather hull, which makes it crowded, but these boats are righting-moment sensitive.
There’s a lot of boat to cross for the maneuvers; how does everyone get up on that hull quickly?
One guy leaves the weather side early to load up a sheet winch and set up the boards. Then the majority of the crew crosses the boat as it’s going head to wind. You leave a couple guys behind to get the board down and then bring them across. We’re looking more to have weight on the high side out of the tack—you need that full power to sheet on the wing and get the acceleration going because your boatspeed deltas between the bottom of the tack and getting going again are vast. Getting the guys up to the high side early to have stability is very important.
How about the helmsman getting from wheel to wheel?
There’s a triple act between Ray [Davies], Dean [Barker], and Glen [Ashby]. Someone’s taking the wheel off Dean, and he’s set up to take the wheel out of the tack. The boats are actually pretty efficient through the tack, unlike most multihulls, because the wing drag is low compared to soft-sail cats.
It appears your rig is farther aft than that of Oracle’s. What’s the tradeoff?
Again, it comes down to structure, and in this case, how much forestay tension you can achieve within the structure. A lot of forestay tension means a lot of stretch in the forestays, backstays, and under-rigging, which means a lot of work in terms of grinder input. The boards are highly loaded, and going through those maneuvers is about keeping wing controls relatively simple. If you have too many controls to get the wing shape to where you want it to be, you’re likely never going to get there.
Is it possible to make the boats simple?
With the AC45s, the courses are pretty small. If you speed it up by 25 percent, it gets really, really small. It will take about 2 minutes to cross the box from one side to the other, so the maneuvers come thick and fast, and then you add extra maneuvers as you interact with the competition. That’s where the huge amount of resources will go in the next few months. The hydraulic systems are a big step up, and getting those tuned so the right controls fall into hand during each maneuver will take a lot of time. The final thing is reliability. Everything is built at such tight weight constraints, so you can’t throw weight at things to make them reliable. It will come from using them and measuring the loads and carefully paring back anything you overdesigned. It’s all about measuring everything that goes on and off the boat: how long the running rigging has been on the boat, how many tacks and jibes a given piece of rigging has been through, and taking it and breaking it on a bench to understand if it’s degrading over time.
What are the fundamental parts of your wing?
Our wing is a two-element wing with a tab, which is where Oracle is as well. With a two-element wing there’s a single aerodynamic slot through the structure. The trim tab controls that space: As the slot opens up, you can achieve higher cambers and more power out of the wing in lighter conditions. Where the subleties are coming in is the ratio between the front element and back element, which influences the downwind performance. We have more wings to build, and the game will be to round out an inventory of toys you can take to the starting line.
How do you effectively alter the wing shape from top to bottom without overcomplicating it?
We need hydraulics in the wing, no doubt about it. The question is how to distribute things around the wing—whether you do that by introducing more hydraulic cylinders farther up, or taking a cable off a cylinder at the bottom and distributing the forces around the wing that way. All the upper control surfaces are controlled by quadrants and cables, so we can do some clever stuff at the bottom. It’ll be interesting to see if anyone else thinks they can get finer control of individual panels and surfaces by going more heavily hydraulic. I read that Artemis has 30-something hydraulic rams in their wing, which implies they’re controlling individual surfaces with rams all over the wing. That’s a complicated system for sure.
What about the foils, and the concept of foiling?
The game is about generating vertical lift off the foils, which is reasonably quick, but it does lead to serious control issues when you get it wrong. It’s quick because it reduces wetted surface area, but the challenge is achieving controllable levels of lift. It’s easy to wheel stand these boats, or fall off the foils with a severe crash. You might survive that crash, but the average speed won’t be good. It’s all about finding and maintaining a high average speed. The boats need a certain amount of foil lift to even be able to bear away, and that ability also comes down to hull volume and freeboard decisions. It’s a complicated part of the puzzle. It will be an interesting part of this competition.
How do you monitor everything that’s happening with the boat, structurally?
We use fiber-optic sensors that are embedded into the composite structure to measure loads. There are about 50 in the platform, another 25 in the wing, six in each daggerboard, and a couple in each rudder. In every hydraulic function, you’re monitoring pressure, and in the winches you’re measuring loads. You’re measuring very accurately the pitch, roll, and heel, and all the various attitudes and speeds of the boat. Boatspeed measurement is a tough one because sometimes there’s not a lot of boat in the water, and it’s hard to find anywhere on the hull that has good, clean, consistent flow. Wind direction, too, is actually very difficult on these boats because the apparent wind angles are so fine downwind that downwind prediction is very tough. There are a lot of technical issues to solve in that area alone.
What realistic speeds can we expect?
You’re going to see VMGs over 30 knots at the top end downwind. What will surprise people is that the performance delta upwind is bigger than the deltas downwind. The pace upwind will certainly be in the 18- to 20-knot range a lot of the time. The guys are already saying there’s no sensation of speed on the boat because everything feels smooth and controlled.