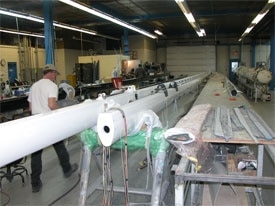
Novis Spars
Outside it’s wet. Slushy remains of lake-effect snowfalls puddle and melt in an unseasonable January thaw-and it’s starting to rain. The days are still short and there are colder ones ahead for those who live along the southern shore of Lake Erie in small towns like Conneaut, Ohio. But inside, 30,000 square feet of an old 70,000 square foot electronics manufacturer is warm, dry, dusty, and filled with long tubes. We’re visiting Fairport Yachts’ spar business, Novis Composites, which didn’t exist 18 months ago and is now building more than 100 carbon spars a year using autoclaves and molds purchased in a liquidation sale from Hi-Tech Composites. David Hulse, formerly a principal at Hi-Tech in North Carolina, is the president of the new operation and gives us the tour along with Fairport COO Tim Jackett. Fairport’s owner, Bill Ross, negotiated the deal that brought Hi-Tech north, picking up an in-house capability to continue his and Jackett’s plan to make Fairport’s Tartan and C&C lines into technology leaders. In the summer of 2003, even before the Conneaut operation was up and running, Fairport announced that all models in 2004 would be delivered with carbon masts. That turned out to be a little gutsy. Hulse spends most of his time on the road and at home in North Carolina, doing the detailed design and engineering drawings and working on custom sales. But he spends at least a couple days every few weeks in Conneaut to help move things down the track. Jackett admits Novis has had a steep learning curve, in part because the local work force doesn’t know sailboats, despite its lakeside location. But they’ve made steady progress and are now shifting their Tartan and C&C production masts from using Hi-Tech’s original carbon molds to three new aluminum molds, which produce a better laminate, requiring little refinishing. The masts are built with hand-laid unidirectional and biaxial pre-preg carbon fiber, with reinforcements on the inside of the mast to further limit the handwork required after molding. The spars are baked in one of two autoclaves, painted with AwlGrip, and then finished with off-the-shelf aluminum spreader brackets, mastheads, sheave boxes, etc. The new molds also allow for a new PVC luff-groove insert that’s capable of holding a bolt rope (for race boats), traditional slugs or slides (for cruisers) or the inexpensive Dutchman batten roller cars (also for cruisers) so additional hardware is unnecessary. As production improves and efficiencies kick in, Jackett says they expect they can deliver a carbon spar for a mid-size cruising boat at a relatively low additional cost (compared to aluminum) of $2,000 to $3,000, a considerable achievement. While Novis serves as Tartan and C&C’s in-house supplier for masts and other carbon parts, Hulse has already begun selling to the custom market on a limited basis. Novis built the mast for Trader, a Transpac 52, and has spars in the works for custom projects up to a 70-foot sled for 2005. Not far from the painting booth, a plastic-draped area holds a tooling project-the mold for the deck of the new C&C 115 is being finished off. And in another part of the sprawling building, a much bigger tooling project is underway. With a skin on it, the thing would definitely float-it’s the male hull plug for Tartan’s new flagship model, the 5100. Jackett’s eyes light up as he considers his latest design taking shape, points out how the station sections are marked on the concrete floor, and describes the process of assembling the plug accurately. Next installment: On the boat-shop floor.