|
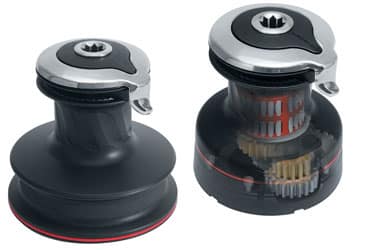
Courtesy of Harken
With its new Radial Winch line, Harken says it’s shaved 25 to 50 percent of the weight off its previous-generation Harken winches. The Quattro line (40ST shown at left) features the new radial drum-grip pattern, as does the 35.2STA (right). Pricing, which was unavailable at press time, is expected to be comparable with previous winches.
Winches, the workhorses of our sail trim, rarely get the attention they deserve. We take them for granted until that unmistakable grinding sound reminds us they’re overdue for a little maintenance. With regular-or even irregular-care, they can last forever, which is why manufacturers rarely redesign them.
However, the big two winch makers-Harken and Lewmar-recently introduced changes that will make you consider whether now might be the time to upgrade that beast you’ve been sweating over each tack and jibe for the past 20 years. The latest iterations are significantly easier to install, maintain, and use. They may even save you a few boatlengths around the track.
Let’s first start with Harken’s Radial Winch line, which the company unveiled at the U.S. Sailboat Show in Annapolis, Md., last October. The development of this new range of Harken winches, says Andrea Morello, Harken Italy’s technical director, was primarily driven by production boatbuilders demanding a winch that was easier, and thus faster, to install. To simplify installation, Harken came up with a patented stud-bolt configuration that only requires the builder to remove the skirt (portion below the red line) from the winch body, insert three stud bolts into slots in the winch base, place the skirt back on, and slide the bolts through three pre-drilled holes in the deck. Tighten the bolts from belowdecks, and voila! No disassembly required.
The design also allows for far easier upgrades to electric- and hydraulically-driven systems: a below-decks electric motor can be attached directly to the central drive shaft without dismounting the winch.
This is all good for the boat manufacturers and their assembly-line efficiency, but for the racer’s enjoyment, the second substantial prong of the Radial Winch’s development was aimed squarely at the drum and how it could better grip modern high-tech line. Traditional abrasive drum faces simply destroy sheet and halyard covers over a typical season.
After testing dozens of different grip patterns (ribs, nobs, etc.), Olaf Harken said at the Annapolis unveiling, Harken engineers determined a diagonal, radial rib pattern worked best. The pattern is described as working like a screw, “driving the wraps down when easing [the sheet] to keep them on the part of the drum where you have the best control.” As you ease a jib sheet, for example, the angle of the ribs stops the sheet from working to the top of the drum, thereby preventing overrides and allowing for a smooth, controlled release as the line exits the winch. This means smoother, quieter sheet easing, and, on distance races, more restful sleep for the off-watch crew.
The radial drum pattern is scaled for each winch size, but it is applied to a wide range of winch types, including the aluminum alloy and chrome offerings, and on the main drum of the Quattro winches-although, the wide-base portion of the drum used for high-speed trimming still has an abrasive face for line grip.
Another important new feature for racers is that the winches are far easier to regularly maintain. The socket, washer, and screw top “snap-fit” together, and when you remove the drum, the composite bearings are held captive in a Delrin cage (red in the bottom image on p. 56). The bearings don’t require lubrication, but, say Harken engineers, an occasional spritz of McLube never hurts.
To improve safety, they’ve combined the winch top and one-piece stripper arm, which now covers the entire top of the winch to prevent fingers and clothing from being pulled into the rotating part. The position of the stripper arm can be adjusted after the winch is mounted. www.harken.com
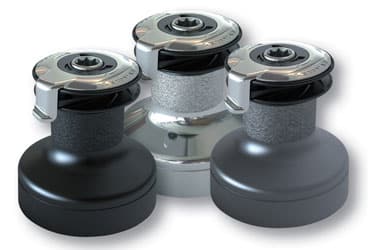
Courtesy of Lewmar|
Lewmar’s updated Evo winch range, uses the same working components of earlier Lewmar winches, but the stainless steel cap/stripper arm was redesigned to prevent inadvertent line snags. Directional arrows on the cap will help novice crews.**|
Lewmar’s Evo Winch
Following on the heels of Harken’s Radial launch, the engineers at Lewmar revealed their Evo Winch range at the Marine Equipment Trade Show in Amsterdam in November. It’s the company’s first-although subtle-winch redesign in 20 years. Thus, Lewmar’s calling it “evolutionary.” Key improvements include easier installation, new sizes, new finishes, and new styling. Internally, they’ve retained the same components.
As it was for Harken, Lewmar’s Evo development partly resulted from a demand from boatbuilders for a quick-install design. Lewmar’s solution is stud-style fastners that screw into the bottom of the bronze base plate. No disassembly is required to install the winch into pre-drilled holes. While they were redesigning this element, Lewmar engineers took the opportunity to tweak a few other components, striving to simplify user maintenance and safety, as well. With the Evo (as it is with previous Lewmar winches), tools are not required to strip the winch: unscrew the top cap by hand and remove the drum to get at the bearing cages and gear clusters. It’s impossible to put it back together incorrectly.
For safety considerations (and aesthetics), the stripper arm completely covers the winch top, which Lewmar says prevents a line from getting trapped above the jaws. And for inexperienced crews, they’ve added a directional arrow on the winch top, showing which way to properly load a line. www.lewmar.com
The Winch Balancing Act: Power versus Speed
With winches, speed and power are inversely related. Faster trimming means less power; high power begets slow trimming. The key determinants of winch/line speed are the gear ratio and the drum size (each revolution of the winch pulls an amount of line equal to the circumference of the drum). A larger drum pulls more line per revolution, but does so with less mechanical advantage (i.e., it requires more effort from the grinder). Here’s a quick comparison of a few comparable models from Harken and Lewmar, using figures provided by the manufacturers. The power ratio figures are calculated for a 10-inch handle.
Model Drum CiRC. (in) Wt. (lbs.) Gear Ratio (2nd) Power Ratio (2nd)
Harken 40.2STA 9.89 8.4 6.28 39.9
Lewmar 40ST 9.15 10.7 5.80 40.20
Harken 50.2STA 13.6 13.2 10.9 50.40
Lewmar 50ST 11.5 19.4 9.0 48.60