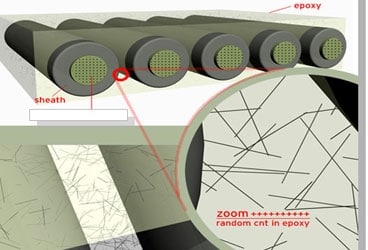
CarbonTubesSt
Nothing today exudes “high-tech” better than carbon fiber. There’s something undeniably seductive about its absolute blackness. Rigs, blocks, sails, hulls, tillers, and even toilets-if it’s on a raceboat, someone will build it out of carbon fiber. There’s no denying that it’s the wonder material of today. But with the recent explosion of carbon nanotube technology, what we consider high-tech is about to go much higher. In other words, if you think your carbon rig is state-of-the-art now, wait for tomorrow.”You can do virtually anything with it,” says Dave Eck, of Forte Carbon Fiber Products, of Ledyard, Conn. “It’s there, and maybe six years from now we’ll all be using it.”It, the incredible carbon nanotube, is a man-made cylindrical carbon thread with a diameter of only one nanometer (that’s one billionth of a meter). Most are a few microns in length (micron being one-millionth of a meter). Under a high-powered microscope you’d mistake one tube for a fleck of dust.Compared to a steel structure of similar size, explains Lance Criscuolo, of Zyvex Performance Materials, of Richardson, Texas, a nanotube is about 100 times stronger at one-sixth the weight. “Inherently, it’s a much stronger material. It’s the strongest material known to man at this point.”Only in the last decade has the potential of carbon nanotube technology has been realized, spawning a worldwide race to capitalize on both its manufacture and applications. Electronic, industrial, and biotech uses aside, you’ll now find nanotubes proliferating in the sports equipment market: golf shafts, tennis rackets, bicycles, baseball bats, and in at least one known raceboat mast, built by Forte specifically for the Synergy 35RL, a 35-foot sportboat built by Synergy Yachts in Seattle.They couldn’t build a rig exclusively of carbon nanotubes, however, says Tony DeLima, of Forte. The nanotubes come in the form of a resin-based addition to the carbon-fiber structure, and an extraordinary one at that. To produce a nanotube-enhanced mast, Forte mixes into its resin formula a syrupy nanotube mixture developed by Zyvex. As the mast is laid up on a mandrel, the nanotube mixture fills the voids between the individual carbon fibers.”The weak spot of a composite is the resin system between the fibers,” says Criscuolo. “The carbon nanotubes fill in that gap and help transfer loads from fiber to fiber.”The result is a tube that has more compressive strength for a given weight than a traditional carbon-fiber tube. “What it does is let me change the laminate schedule because I only need x amount of strength on a mast anyway,” says Eck. “That means using the nanotubes I can lower my laminate schedule, which allows me to make a lighter spar.”In it’s own independent research, conducted before building the Synergy mast, Forte found that nanotube-enhanced tubes showed a 15-percent increase in compression strength. “That’s significant,” says DeLima. “For our everyday tubes we use intermediate-modulus fibers, and with the addition of the nanotubes, we got a high-modulus-carbon type of compression strength. There’s a huge difference in price between the different modulus carbons-they can go from $14 per pound [for the intermediate] to $49 per pound [for high-modulus]. So with this little bit of carbon nanotubes we are able to affect the same performance increase with a much smaller price increase. It only adds about 20 percent to the cost.”According to Criscuolo, the test results they’re seeing at Zyvex, which purports to be the only company capable of “functionalizing” the carbon nanotubes from their black-powder state (i.e. making them usable) are significant as well: 17- to 20-percent increase in shear strength, a flexural strength increase of about 15 percent, and a compression strength increase as high as 34 percent. This should enable builders to either build a spar with more compressive strength without adding weight, or building a lighter spar without changing the strength. “The real benefit to the customer,” says Eck, “is that now we can really lighten things up.”While the technology is there for the taking, however, the market, adds Eck, is not-at least not yet. “It’s going to be a while before we see much activity,” he says. “Because of the nature of one-design classes, the spars we build with this stuff will be custom orders. The market now is for the one-off guys that are trying to make their boats that much faster. The extra little cost of enhancing with the nanotubes is not that dramatic.”But the potential uses of nanotube-enhanced composites extend far beyond masts: there’s booms, spinnaker poles, standing rigging, and certainly hardware and hulls. “You could get the same effect by blending nanotubes with fiberglass,” says Criscuolo. “And this would let you take some material out of the boat while keeping the strength for the same weight. You’d get a significant improvement in impact, flex, and all those other things. It can go with chopped fiber, unidirectional, you name it.”