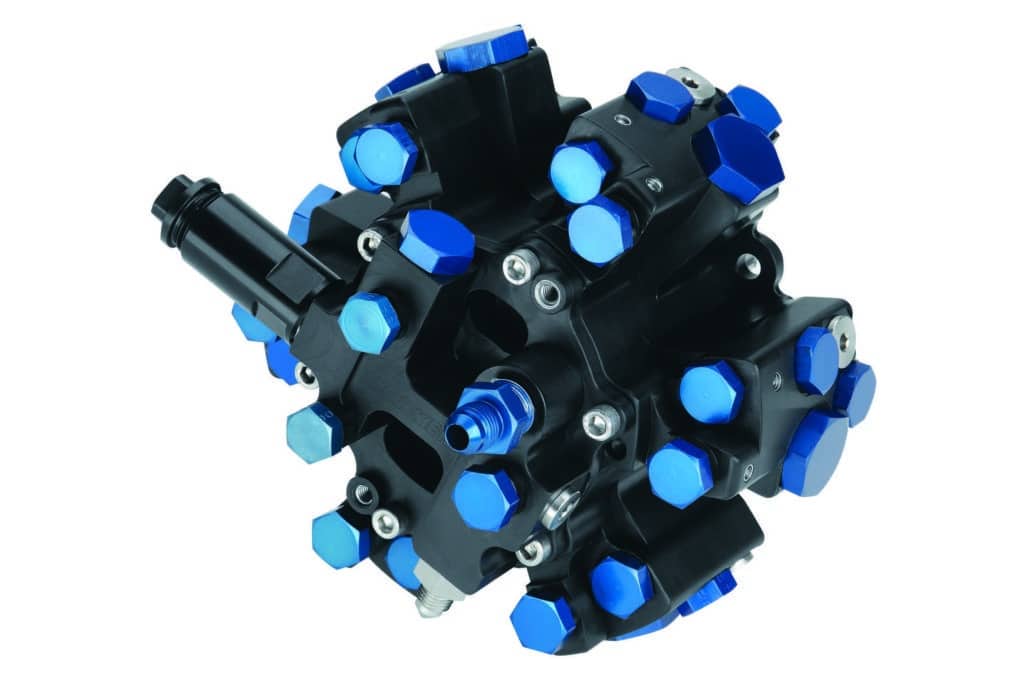
The America’s Cup grinder’s job has been transformed over the last two Cup cycles whereas the grinding is now virtually nonstop. What’s up with that? Two words: hydraulic pressure.
Eighty-percent or more of the energy spent grinding is invested in moving hydraulic fluid around the boat. The need for hydraulic pressure has been driven by the increasing sophistication of the boats, specifically by the number of controls that need adjustment, above and below the water, sometimes under extreme loads.
Every team sails its boat differently. Harken has developed and supplied solutions based upon specific design briefs the teams issue. Generally speaking, on the AC50 the functions controlled by hydraulic cylinders include: the two foils (height, cant, rake), the two rudders (rake), and wing control (twist, camber, invert).
The foil-pitch solution is used most frequently. This hydraulic control’s stroke is short, and flow requirement is minimal, but it’s used by the helmsman to balance the boat’s fore and aft trim, so it has to react quickly. The foil-height solution typically requires the highest actuation speed. The windward foil towers above the deck, revealing a cylinder with an extraordinarily long stroke. As a result, this system requires the largest oil flow and highest actuation speed.
It’s no coincidence then that the most sophisticated hydraulic component Harken sells for AC application is the AC35 Radial Pump, pictured above. It’s a three-speed 20-piston pump that bears a striking similarity to a radial piston-driven aircraft engine, though in a much smaller size. There are four of these “hearts” onboard the boats – mounted to the outside of the Harken MX Pedestals in each hull. This is the core of the system, and just like the heart of the grinder at the pedestal, the Radial Pump is the muscle pumping blood to a champion racehorse.
– Bill Faude and Mark Wiss, of Harken